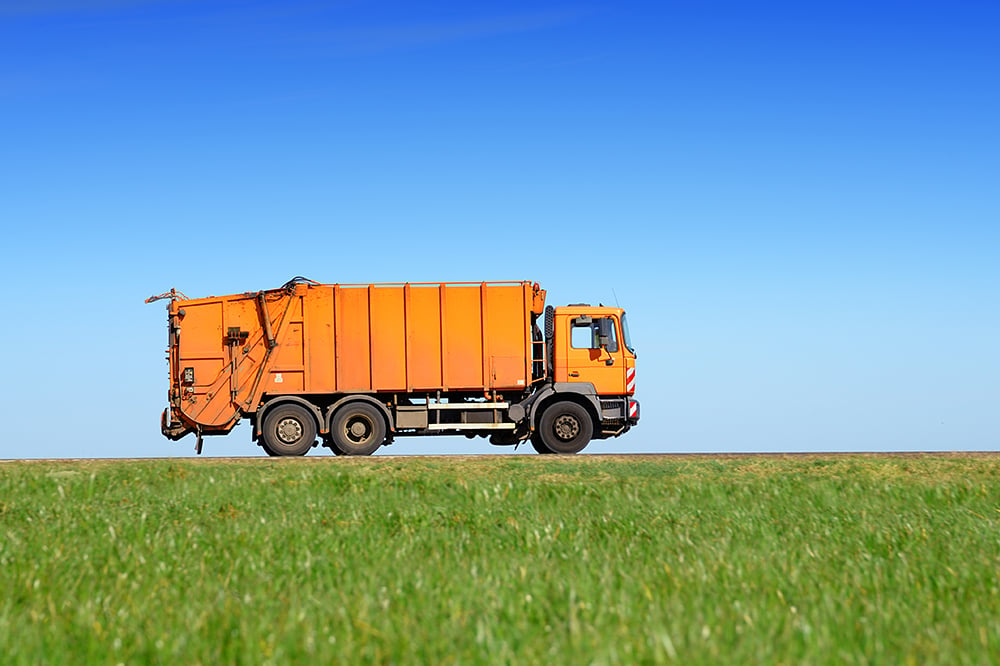
Risk & Insurance
A Proactive Risk Approach Can Help Stem Injuries
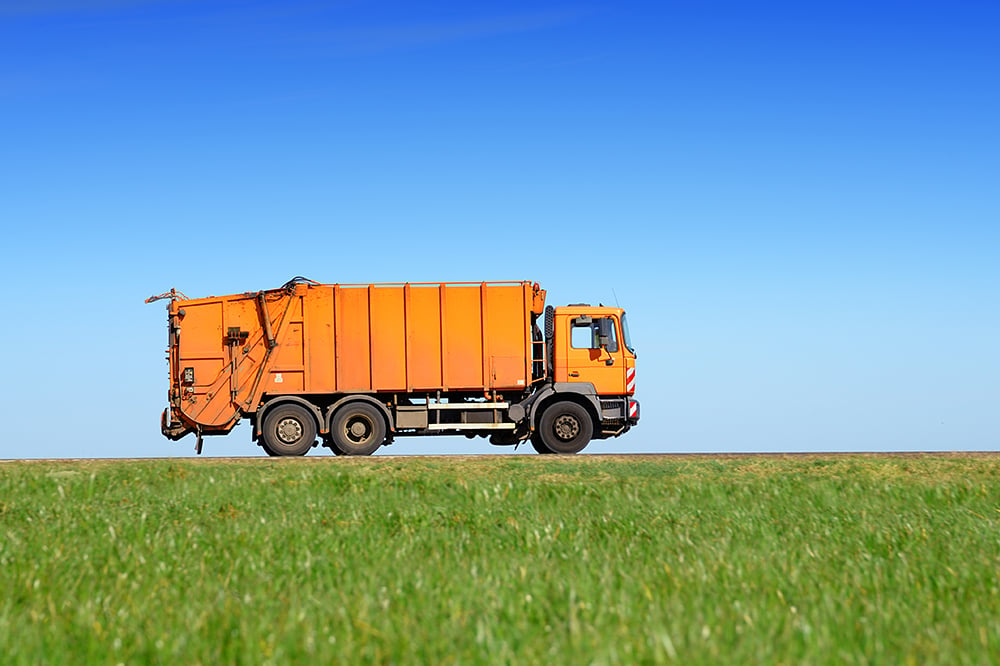
The economy simply can no longer be the excuse as to why safety is not a top-tier priority in the waste and recycling industry. During recent challenging times, companies of all shapes and sizes elected to adopt a cost-cutting focus simply to survive, causing many to rethink their investments (both time and money) in programs related to fleet management and safety.
In 2013 as a result, the number of industry fatalities spiked by more than 25 percent, which boosted the waste-and-recycling industry to the fifth most dangerous profession (up one spot from the prior year). All workers in this industry should be focused on how to increase the odds of getting drivers home safely to their families each day.
Traditional Approaches to Injuries
Mindsets around safety in our industry have frequently been based from “nature of the beast” to “the employee has to be held accountable… I can’t hold their hand.” Driving a compactor truck loaded with nearly 10 tons of waste is an extremely dangerous profession.
Any profession can be made dangerous while operating with a laissez faire attitude. Safety starts at the top of the organizational chart and must be constantly visible. If safety is driven home on a routine basis with a set of professionally crafted operating procedures, the waste industry can be thought of in the same light as our other trucking brethren. Insisting that a driver is 100 percent to blame and responsible is like saying a sales individual is in charge of the overall financial performance of the company. While they drive growth that directly impacts the bottom line, they are only part of the solution; not the end all/be all.
The most prevalent and damaging company environment is the all too familiar lip service to risk and injury mitigation efforts. In this scenario, some signs are put up in the break room, and a safety-first pizza lunch is provided every once in a while. These gestures are not entirely wrong, but they must be included in a much larger overall safety-imperative effort. One driver, making one bad decision, can completely change the entire direction of a company.
Damaging Consequences from Traditional Mindsets
There are significant, and often unrecognized, outcomes from injuries within our industry, including, but not limited to, the following:
- Increased out-of-pocket expenses
- The inability to bid on certain jobs
- Rising insurance premiums
- Declining customer satisfaction and retention rates
- Weakening driver attraction/retention and absenteeism
A company doing the bare minimum in regards to protecting its most essential assets (its people) is much more likely to experience downward spiraling financial performance. The next time a garbage truck passes, wonder whether or not the team carrying out that service is satisfied with what they are doing or if they’re just putting in their time. It might change how close you are willing to drive hugging the center line.
Due to being in the high-frequency/high-severity quadrant when it comes to employee injuries, waste and recycling companies are discovering it is increasingly difficult to find more than a handful of insurance carriers that provide coverage for our industry. Carriers are funny—fond of premiums. Excessive claims? Not so much. The rising litigation costs, followed by increasing fatality rates, are ugly to see. Barring companies embracing the safety imperative, as opposed to giving it lip service, these trends will only get worse.
The Good News
The waste industry does have a lot of things going for it as far as finding well qualified drivers. They are home at night. The hours worked often leave free time during the middle of the day for employees to take care of personal needs. Drivers are familiar with routes and work within a limited radius. Helpers are used in residential vehicles. And the weather does not affect their weekly number of hours; as is often the case in other trucking industries. The waste and recycling industry is generally thought of as stable in terms of hours worked and providing steady pay. This being said, employees have to know that they are regarded as valuable tools that need to be consistently sharpened.
So how do you know you have an effective program in place that will generate long-term success, stability, and reverse the trend of profit drain? It all starts with the Proactive Risk Approach (PRA). This PRA is based on a sequential and protected process.
- Assess your current situation and find the deficiencies. You’re only as good as your weakest link.
- After the gap identification, address the low-hanging-fruit improvement opportunities you’ve known about for a while and have put off.
- The most important aspect of a proficient PRA is to not stop here. Companies must invest in a multi-prong approach that addresses the true problems rather than simply masking the symptoms.
Core Elements of an Effective PRA
These additional steps are essential:
Select Drivers Carefully
This is an ongoing practice—not an event. What happens if you lose your best driver tomorrow? How do you replace them? Creating a list of qualified prospects and working it frequently allows for a much less severe situation than starting from scratch. In the hiring process, lowering your standards should never be an option. If you don’t find a worthy hire, don’t settle or force a hire.
Create a Safety-First CultureSuch an environment cannot be faked. The buy-in must come from the top and trickle down. Keep in mind your team members will listen to what you say far less than they’ll watch what you do.
Keep Safety Training Ongoing
Training is not reserved for new hires only; it must be an ongoing initiative, be regularly enhanced, and be designed to enhance and encourage everyone to be their best at all times Creating open communication with all employees strengthens any culture of safety.
Maintain Visibility
The PRA cannot be a flavor-of-the-month program. Employees must know who they can and should turn to and should be encouraged to identify hazards or best practices. Employees are the ones who truly establish and carry out company culture.
Monitor Your Results
Any effective PRA must quantify the program outcomes. This can be done in a number of ways (e.g., sick days taken, tardiness, increased retention, customer-service ratings, yards collected per hour, maintenance dollars versus fines, etc.). Share metrics with your employees to spark a friendly competition.
Recognize and Reward Improved Performance
Incentives must be provided for clean MVRs and roadside inspections, turning in all paperwork correctly and on time, improved customer-retention rates, customer surveys, etc.
Assess Your Insurance Program Regularly
This ensures the retention versus transfer balance of potential threats in focus and will gauge if your limits are optimal given current market conditions and risk appetite.
Continue to Fine-tune
There is no one program that will be perfect for every company, and even if there were, things change. The culture of the company is going to evolve, so be flexible in finding what works, as long as safety remains top of mind.
Most companies don’t have adequate resources to establish and maintain a PRA program alone. It’s essential to partner with the right team, so seek out firms with insurance-industry experience, in-house resources, knowledge and working capital to provide external resources, and a documented track record of success mitigating injuries and overall loss with waste/hauling and recycling clients. It’s never too early to improve your overall safety program, as the short- and long-term returns are excellent. Ramp up your safety culture driven by a PRA, and you’ll experience an exceptional ROI.
About the Authors
Steven Billings is a risk advisor in Relation’s waste-management practice focused in alternative risk solutions and value-added services. He can be reached on LinkedIn, via email at [email protected] or via phone (704) 688-1285.
George H. Lucas, Ph.D., is director of coaching and learning at Schul + Baker Partners of Dallas, TX. He can be reach via email at [email protected] or via phone at (469) 291-5493.
This article originally appeared on the Waste360 website.